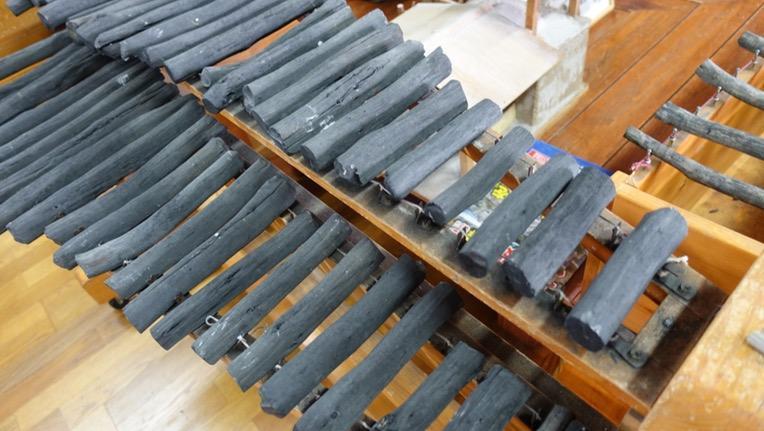
Binchotan Charcoal: How it's Made and Why it's Awesome
For the beginners, Mike has covered most of the basics about the Binchotan charcoal in this blog here. The blog you are currently reading goes much deeper into the details of how charcoal is made; for the bincho-nerd's among us. In this article I will cover how Binchotan is made and where it comes from. Check out our guide to Binchotan grades if you want to learn about the different types!
Binchotan(備長炭) is named after a charcoal maker in Tanabe, Wakayama prefecture, Bicchuya Chozaemon (備中屋長左衛門), who started selling this type of charcoal (Tan or 炭) in late 17th Century. Wakayama prefecture was called Kishu before the Meiji restoration in 1868, so the Binchotan produced in the area is called Kishu Binchotan to differentiate it from other Binchotan varieties. Originally Binchotan was only from Wakayama, but some charcoal makers have moved to other areas of Japan, such as Tosa and even further to Miyazaki (Hyuga), seeking a specific type of wood called Ubame Kashi or Ubame Oak (ウバメ樫).
Ubame oak is harder, with a tighter grain than regular oak trees, and is preferred by Binchotan makers. All of the various Binchotan makers are located in areas with similar terrain and lattitudes, as Ubame oak usually grows in hilly and hard-to-reach areas, which makes harvesting this type of wood more challenging than regular oak.
Ubame can be written in several different kanji, usually either 姥目 (elderly woman’s eye) or 馬目 (horse's eye). These are in reference to the buds of the trees that look like wrinkly eyes.
I don’t know about you, but I’ve always been curious about the process of making charcoal. When I burn wood in a fire pit, all I end up with is ashes rather than something dense and refined. When I heard that to make charcoal, the oak is burned at 1000 degrees centigrade, I thought everything would just burn into ashes. The key to not letting that happen is oxygen, or rather, the lack thereof. When you burn wood in an open environment, oxygen in the air will bond with carbon in the wood, creating CO2 and leaving behind ashes. However, if you limit the available oxygen when burning, it will evaporate the water out from the wood, resulting in charcoal! Binchotan and other types of charcoal are, for the most part, made in similar procedures — except for the final part of the process, which we will get to later.
Any industry that relies on nature has to be careful of how much they consume because over-harvesting would threaten the industry. The same, of course, can be said of Binchotan makers. They rely almost 100% on natural resources and have learned over the years just how many trees they can fell per year without damaging the forest and their industry. Despite this, with the recent increase in popularity and demand for Binchotan, some companies have sadly ignored their ecological traditions and have harvested more trees than they can recover, so there is a threat to the supply of Ubame Oak. We are happy to say that our supplier remains committed to sustainable harvesting!
How is Binchotan Charcoal Made?
The first step to making charcoal is, of course, going out into the forest and chopping down trees. As mentioned above, this Ubame oak prefers to be grown in hilly areas so it takes skill and experience to harvest. Once the Binchotan maker has enough wood, they bundle it up and carry it back to the factory. This is all done by hand due to the terrain. Additionally, the trees do not grow straight, so in order to comfortably bundle the wood they need to make incisions into trees and insert wooden wedges to make them straight. Thicker trees are even split in half. All said, it’s a lot of hard work.
These bundles then go into a special kiln, layered very tidy and snug in an upright position. These kilns are big enough for a person to walk into! Once they’ve layered the wood in, they add a less dense wood as a starter fuel that will light and burn more quickly. They light the whole thing and seal in the opening with brick and mortar, gradually over a nine hour period. The leave 4 small holes: two at the top of the kiln and two at the bottom, for airflow to the fire and to release steam. In order to remove all moisture from the wood, they do a long, controlled burn at lower temperatures that takes six or seven days. During this process, white steam can be seen coming up from the chimney of the factory. Once all the steam is gone, the wood has become charcoal.
From here, regular charcoal would be made by closing all the openings, starving the fire of oxygen and snuffing it out. If all they wanted was regular charcoal then they would let it cool down and remove the finished charcoal, but Binchotan goes through an extra step. This step is a big part of what makes Binchotan so special.
This final process is called “Seiren” 精錬, or refining. A Binchotan maker, instead of closing the opening to snuff out the fire, will make more openings in the kiln, gradually adding more airflow. This process has to be done at a very gradual pace, as a rapid increase of oxygen inside the kiln would burn everything into ashes and ruin their hard work. Too slow, and the Binchotan won't turn out quite right. This final process takes between 24 to 48 hours, during which the internal temperature reaches 1000 degrees centigrade. This process burns off bark and makes the charcoal denser, tighter, harder, and more pure in carbon content. Binchotan charcoal is 95% or more pure carbon, whereas regular charcoals are around 75%.
The Binchotan maker then starts to take hot charcoal out of kiln. If they extinguished the fire using the same process as regular charcoal makers, by the time the kiln cools all that would be left in the kiln is ashes. They have to empty the kiln while the coals are hot! As they empty the kiln, they cover the Binchotan with sand and ashes to cool them down gradually. The dust that coats the charcoal is the reason why Binchotan is called “white charcoal”.
The whole process takes up to 10 days and produces about only 600kg of Binchotan per batch. A lot of mass is lost in the process: the weight of the charcoal at the end is one-tenth the wood that goes in, not to mention the wood burned as fuel for the kiln. Binchotan making requires immense skill and is a very labour-intensive process, passed down through generations. Why would someone go to such great lengths, dedicating their life to make charcoal? Because it's the best. Binchotan burns hotter, cleaner, and far longer than any other charcoal. It radiates infrared light that cooks food more evenly, and it's intense heat vaporizes drippings to create a magical smokiness in your food. It's magic, and we're honoured to bring the product of these traditions to our customers in Canada.
If you’d like to see the process for yourself, here are links to great videos from our Binchotan supplier, Okazaki-san. They are quite long (6 videos, and they are about 20min. each) and have no English subtitles, but now that you’ve read this article, we bet you’d get some enjoyment out of seeing it all happen.
Here is Video Number 6, go checkout the first 5 Here!